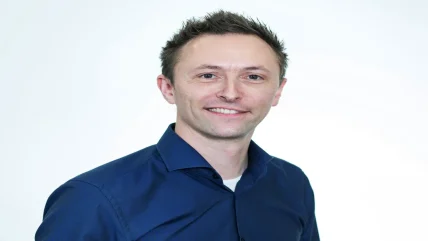
Today’s fleet operators are faced with an increasing number of pressures – rising costs, a growing urgency to go green and the need to keep vehicles operating safely on the roads for longer. While it can be a challenge to balance these issues, one area that operators can focus their efforts to optimise their fleet is maintenance.
The state of play
As the transport industry strives towards a carbon neutral future, there are a growing number of clean air zones being enforced across the nation and an expansion of London’s ultra-low emissions zone set to take force this August. Vehicles driving in these areas will be expected to meet minimum emissions standards and those that don’t, will be required to pay a daily charge.
This presents a challenge for fleets of older and less efficient vehicles. While there is the option to go green and move to electric vehicles, for managers of ICE fleets unable to transition to alternative fuel just yet, or those who are needing to make the switch in stages, the health and longevity of their vehicles need to remain a top priority.
In addition to these associated emissions charges, fleet managers are having to be more financially strategic while the cost of fuel remains considerably high and corporation tax continues to rise. As such, keeping fleets in top working order for longer, is imperative to organisational success.
Maintaining a longer life for fleets
Naturally, to get the most out of a vehicle and ensure it remains safe to drive, it has to be well maintained. Vehicle failures due to poor maintenance programmes can lead to unexpected project delays, wasted time, financial losses and in the worst case, unsafe driving and accidents.
Vehicle maintenance can be broken down into two types: preventative and predictive. Preventative maintenance follows a schedule, often based on the manufacturer’s recommendations of certain time and mileage benchmarks. Predictive maintenance is based on real-world equipment condition and usage. It uses sensors and connected assets to forecast when a vehicle or asset might break down or require repair, helping to reduce the guesswork and unpredictability of maintenance while also optimising a vehicle’s condition.
Digital fleet maintenance software that is integrated with a vehicle’s telematics system, can automatically track maintenance schedules using vehicle odometer and engine hours data, as well as forecast repairs to improve vehicle availability and performance. This enables fleet managers to build and assign accurate, digital maintenance schedules to specific vehicles, a group of vehicles or an entire fleet.
By digitising maintenance planning, fleet operators can streamline the process of setting maintenance schedules and create visibility that means maintenance can be plotted around business needs. In turn, this can reduce the need to rent vehicles or equipment and part with any unnecessary costs.
Additionally, fleet operators often find that maintenance periods are shorter, as visibility into future maintenance needs means that parts can be pre-ordered and delivery delays avoided. By keeping on top of scheduled maintenance and quickly resolving issues, vehicles are inherently healthier, safer and go on to live for longer.
Choosing the right tech
When reviewing fleet maintenance software, it is important that operators evaluate how the tools will aid the business to achieve its maintenance objectives. These can include minimising vehicle and equipment downtime, catching potential problems early, reducing paperwork and streamlining the maintenance process.
A tool with an integrated calendar lets users set manufacturer-suggested or custom maintenance intervals and instant maintenance alerts. Real-time engine diagnostics provide critical insights that enable fleet operators to make informed decisions about a fleets’ performance and whether they should be on the road. The immediate nature of predictive maintenance software means that issues are picked up quickly before they turn into bigger problems that could directly impact vehicle downtime and work schedules.
In order to respond quickly and accurately to a fleet’s maintenance needs, it’s helpful to select a tool that provides integration with a digital app, as well as customisation functions. This allows fleet operators to set up pre and post trip inspections for any vehicle type and instantly record the results, with failures triggering alerts that can be quickly acted upon. The interface should be simple to use and provide prompts for actions that need to be taken, while automatically feeding checklist data into the fleet management software.
When searching for a new software partner, such as a provider of a fleet management system, fleet operators should interview vendors to learn about the tool’s features and a demonstration before onboarding is important to ensure that the right solution for the business has been selected.
Barney Goffer is UK product manager at Teletrac Navman UK