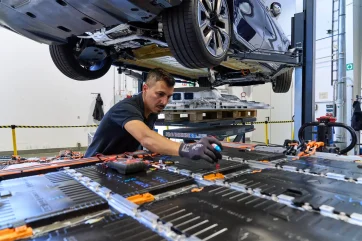
More than 1.25m EVs have been registered in the UK this decade alone, the lion’s share of which have gone to fleets – and we did not count hybrids. Most of those will still be on the road, as will the majority of early mainstream EVs that have been around since the Nissan Leaf’s 2010 debut, but save for those with truly cherished classic status, anything with a V5 will one day head for the great scrapyard in the sky.
Or it would if it had an internal combustion engine. The EU Batteries Regulation requires manufacturers to recover and recycle batteries when an electric vehicle is retired which, these days, is more likely due to an accident than ageing. The UK broadly adheres to the same regulation, and it is illegal to either incinerate batteries or send them to landfill.
It bucks the established trend of dead vehicles heading to dismantlers to be carved up for parts. That is not to say an ageing or written-off EV bears nothing of value, but for the same reason that it is generally cheaper to maintain than an equivalent petrol or diesel car, an EV has much less in the way of salvageable components, such as catalytic converters or gearboxes. Present one to a scrapyard, and the response will probably be ‘no, thanks’, or a bill.
Precious metals
You might not be able to unbolt them like you can an exhaust, but the materials that make up a battery are really rather valuable, so the recycling incentive transcends environmental regulations.
Alan Colledge, technical director at Lithium Battery Recycling, explains: “If we send batteries wholesale to European offtake, we get a gate fee [a disposal charge paid to a waste processing facility], whereas if we’re able to get into the materials, we’ve got copper and aluminium, we’ve got nickel, we’ve got cobalt – we’ve got materials in there that could be a good commodity income.”
Specialists such as Lithium are now receiving damaged and defective batteries from the likes of OEMs, motorsport companies, vehicle testing organisations and disposal sites for processing, which can start by using specialist discharge equipment to sap the remaining power.
“We’ve got regenerative DC to AC conversion loads, and we connect the batteries up to do a deep discharge,” explains Colledge. “We have to bypass a battery management system, because that’s there to keep the battery alive. We want to kill it off.”
It is chiefly a safety measure to avoid ‘thermal runaway’, which is when the components inside a damaged cell make contact and generate heat, the upshots of which could be venting, expansion or full-on combustion.
Step two is shredding, which does what it says on the tin: it breaks down the battery into small pieces that are easier to process. Lithium’s system uses a vacuum of airflow, which suits discharged batteries and allows them to be shredded dry. It is an energy-heavy process, and specialists often look to recovery techniques to claw back some of the costs. Lithium absorbs power from the discharged batteries and channels it into the hardware – and into its pair of 11kW electric vehicle chargers.
“Today, 36% of our energy has come from recovered batteries and we have discharged a total of 70 kilowatts of energy,” says Colledge, tapping an app on his phone during our video call to illustrate the real-time energy performance. “It’s a nice by-product to have, but it is extremely necessary.”
It is also possible to dismantle live batteries (i.e. those that still contain charge) with wet shredding, which uses a curtain of water to discharge them. Yet another technique for shredding live batteries is a chamber filled with an inert gas, such as nitrogen, which prevents combustion by starving them of oxygen.
The latter technique is employed by fellow UK battery recycling specialist Recyclus: “We process [the battery] under liquid nitrogen and that enables us to shred it in a dry environment,” says director and co-founder Robin Brundle. “We then add a little bit of low-energy heat to vaporise the electrolytes, then capture it and condense it back down to a liquid… then we process the rest of the material and we end up with the black mass.”
Refine art
Black mass is a dark, talcum-powder-like substance containing – among other less valuable elements – the battery’s remaining nickel, cobalt, manganese and lithium. It is the quarry from the shredding but needs refining before the minerals can be whipped back into a usable condition – think crude oil before it becomes petrol (the phrase ‘black gold’ arguably applies to both).
That is where stage three comes in: processing black mass to extract the raw materials. The two dominant techniques are hydrometallurgical and pyrometallurgical; the former is common in China, but facilities also exist in Europe, the US and South Korea. The black mass is treated with a solvent to extract the minerals (a process known as leaching) which are then separated. This is generally considered the superior method, because it recovers more than 90% of the raw materials.
Pyrometallurgy is more common in Europe. It breaks down black mass by heating it to extremely high temperatures – up to 1,500 degrees Celsius – which separates the minerals, and lithium-ion batteries are among its commonest applications. It primarily recovers cobalt and nickel and copper, but not the full amount, and the losses are greater than those of hydrometallurgy, chiefly because the lithium is lost in the process.
Stage four squares the circle – or, rather, the circular economy – and constitutes further processing of the salvaged materials at a mineral refinement facility, to the point where they can be used in a new battery.
The UK currently has no metallurgical facilities, so our black mass is exported, and stage three onwards takes place entirely overseas. The government has identified it as both a weak spot and a prospect in homegrown battery recycling.
In 2022, then-chief scientific advisor, Patrick Vallance (now minister of state for science, research and innovation), chaired an industry roundtable event entitled ‘What are the technical and policy barriers to increasing EV battery recycling capacity in the UK?’. The meeting notes described recovery and separation as “scaling well” and black mass processing and refining as “far behind,” other countries, especially China, which has a mature market for both battery production and recycling.
The government also said the “recovery of black mass and other battery materials into sustainable materials, and how recyclate can be made into batteries are the biggest opportunities for the UK”. It cited research by environmental think tank Green Alliance, which claimed the UK’s fleet of electric cars and vans contained more than 1,400 tonnes of lithium and 800 tonnes of cobalt, worth £26.3m and £31.5m respectively, and enough to make 220,000 EV batteries.
It also pointed to a calculation by the Advanced Propulsion Centre (APC) which suggested manufacturing scrap from the scale-up of UK gigafactories and from end-of-life vehicles could generate 28,000 tonnes of potentially reusable battery waste.
It added that “by 2040 recycled battery waste from end-of-life vehicles and manufacturing waste could supply enough cathode materials to produce 60GWh of new batteries.” However, that was before the closure of much-hyped startup battery manufacturer Britishvolt, which went into liquidation in November 2024. While there are other lithium battery producers in the UK, APC’s estimate may have been optimistic.
Home front
Work is underway to establish the latter stages of battery recycling in the UK, and Brundle is among those with an eye on a homegrown black mass processing facility: “We have bought a consortium together of a UK car company, ourselves and a black mass separator,” he explains. “We believe that, within 18 months, we’ll be well on the way to having black mass separation here in the UK.”
While the opportunities mount, scale remains a challenge for UK battery recyclers. Recyclus describes itself as the UK’s first industrial-scale lithium-ion battery recycler, with an environmental permit to handle 22,000 tonnes of waste batteries a year, but such capacity is in anticipation of what is to come. Colledge says his firm shredded around 260 tonnes of batteries last year and would like a tenfold increase as soon as possible.
The current problem, as he explains, is that even early mainstream EVs are sturdy enough to still be in service.
“Off the top of my head, around about 23,500 [electric] cars were sold from 2010 to 2013, so that’s about 5,000 tonnes of batteries – and those are cars which you could still buy on Auto Trader. A 2011 Nissan Leaf or a BMW i3 – they’re going to go through the vehicle recycling process first – and a lot of those haven’t even reached banger status.”
Volume will come, though, and fleets need only look at their own buying habits over the past decade or so for a glimpse of its origins. The Mitsubishi Outlander PHEV launched in 2014 and, controversial charging/taxation habits aside, was a knockout with corporate buyers. Popular pure-electric models, such as the Jaguar I-Pace and Tesla’s more accessible Model 3, were with us by 2018 then, in 2020, we got record-low company car tax rates for EVs. Get past the post-pandemic semiconductor shortages, and you are talking about a lot of batteries.